

The first two steps in this process can be automated, but the last two involve a more hands-on approach that revolve around physically repairing the problem and investigating further into what could be the root cause. Solve the root cause issue with investigation tactics.Pinpoint errors or abnormalities within products.JikodaĪ simple and fast explanation of Jikoda is “automation with a human touch.” Jikoda is an important Lean strategy that TPS uses for the following four steps: Aside from the above principles that the Toyota way is built upon, TPS also relies on two other primary concepts: Jikoda and JIT production. When implemented properly, TPS and its corresponding fourteen principles, can have a positive impact on the entire manufacturing process. Staying true to additional Lean techniques such as Kaizen, Six Sigma, Kanban, and the Shingo method will only benefit the business in their quest for continuous improvements. Make sure to explore all possible alternatives before coming to a consensus on the final decision. Make educated decisions but implement changes quickly.Taking a trip to the factory floor to converse with workers reveals opportunities for improvements. Observe and reflect for improvements by using techniques such as Gemba.Respect all suppliers and stakeholders as they are an extension of the business.Develop excellent people and teams to create a stable company culture.A leader is a role model for everyone else working in the facility, which in turn positively affects the established company culture. Teach leaders to live and pass on the TPS philosophy.The point here is to use technology to support those who are working rather than replacing people with technology. Use visual tools to indicate special procedures, warn employees of dangerous conditions, and to create a more organized workspace.This works to eliminate any confusion and boosts efforts for continuous improvement. Standardize workplace tasks to give employees a reliable job method.This will help create quality product the first time around.
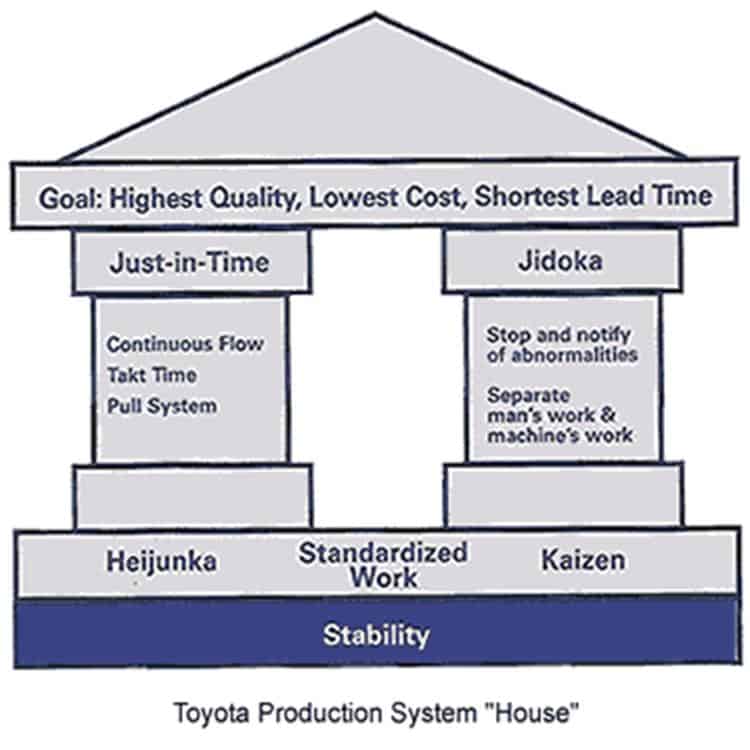
Build a positive company culture that assists the company with fixing problems as soon as they occur.Level the workload to prevent burnout, this is referred to as heijunka or “work like a tortoise, not the hare.”.This is the basic idea of Just-in-Time production as it reduces inventory and enables the company to satisfy the customer’s demands.
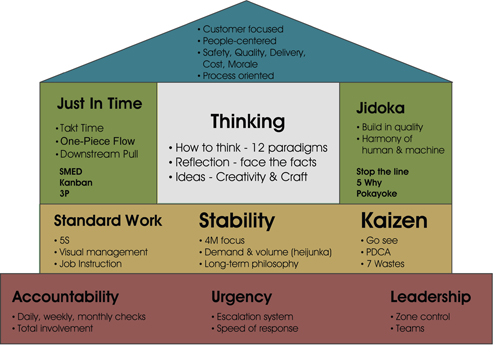
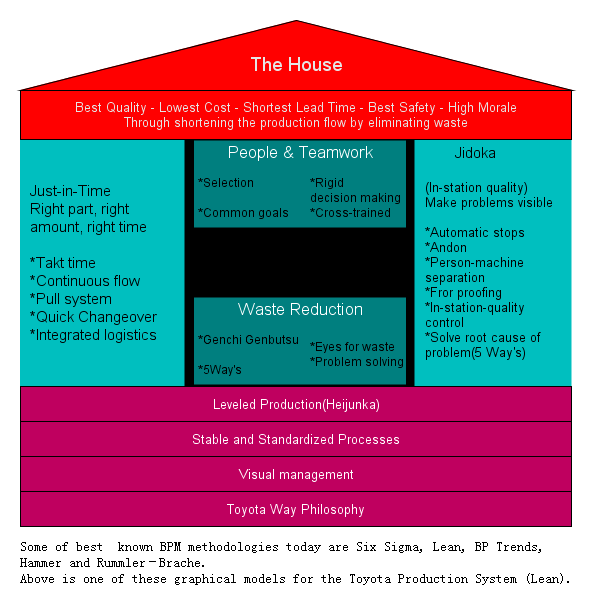
Developed by the Japanese auto manufacturing company Toyota, this Lean method has a special focus on auto manufacturing. The Toyota Production System, also referred to as TPS, is a strategy that helps organize the manufacturing and logistical aspects of a business. History of the Toyota Production System.
